Rapid prototyping is a huge part of product development. Every product, from gadgets to industrial equipment, goes through a testing phase. This stage allows designers to spot problems early and make changes before mass production. One method leading the charge in rapid prototyping is CNC machining. CNC prototypes are gaining ground for a simple reason—they are reliable, quick, and offer unmatched accuracy.
What is Rapid Prototyping?
Rapid prototyping is all about bringing an idea to life quickly. Designers and engineers create models, which they tweak and refine to get as close to the final product as possible. Traditionally, this involved manual methods that took time. But now, technology allows for faster, more accurate results. Using machines to create models, rapid prototyping helps teams visualize and test designs in real-time, cutting down on costs and time.
The Rise of CNC Prototypes in Manufacturing
CNC stands for Computer Numerical Control. These machines take computer-generated designs and turn them into physical objects. A CNC machine is programmed with precise details, allowing it to cut, drill, and carve out a prototype with minimal human intervention. The rise of CNC prototypes in the industry has transformed how companies approach product development. With the ability to create parts with exact measurements, CNC machines offer a level of consistency that’s hard to beat.
Why CNC Machines are Dominating Rapid Prototyping
CNC machines are not a new invention, but their application in rapid prototyping has become more common. Here’s why CNC prototypes are leading the future of rapid prototyping:
Accuracy is Everything
CNC machines can carve out intricate shapes and designs with extreme accuracy. The precision goes down to fractions of a millimeter. This means prototypes closely match the digital design without needing lots of tweaks. In industries where precision is critical—like aerospace, automotive, and medical—this accuracy is crucial.
Faster Turnaround Time
Speed matters in rapid prototyping. When you’re racing against the clock, waiting for weeks isn’t an option. CNC machines significantly cut down on production time. The automated process can quickly transform a digital model into a physical object, allowing teams to iterate faster.
Durable Prototypes for Better Testing
Not all prototypes are equal. Some are just rough drafts, while others need to withstand rigorous testing. CNC prototypes can be made from strong, durable materials like aluminum, stainless steel, and hard plastics. This means designers can run more demanding tests without the prototype breaking apart. A durable prototype is a better representation of what the final product will look like.
Versatile Material Choices
CNC machines work with a wide variety of materials. This includes metals, plastics, wood, and composites. The flexibility of materials allows for better experimentation. If a design needs to be tested in metal and then in plastic, CNC machines make it easy to switch materials without overhauling the entire process.
Cost Efficiency Over Time
While CNC machining might have higher upfront costs compared to other methods, it saves money in the long run. The accuracy reduces the number of prototypes needed, and the fast turnaround means fewer delays.
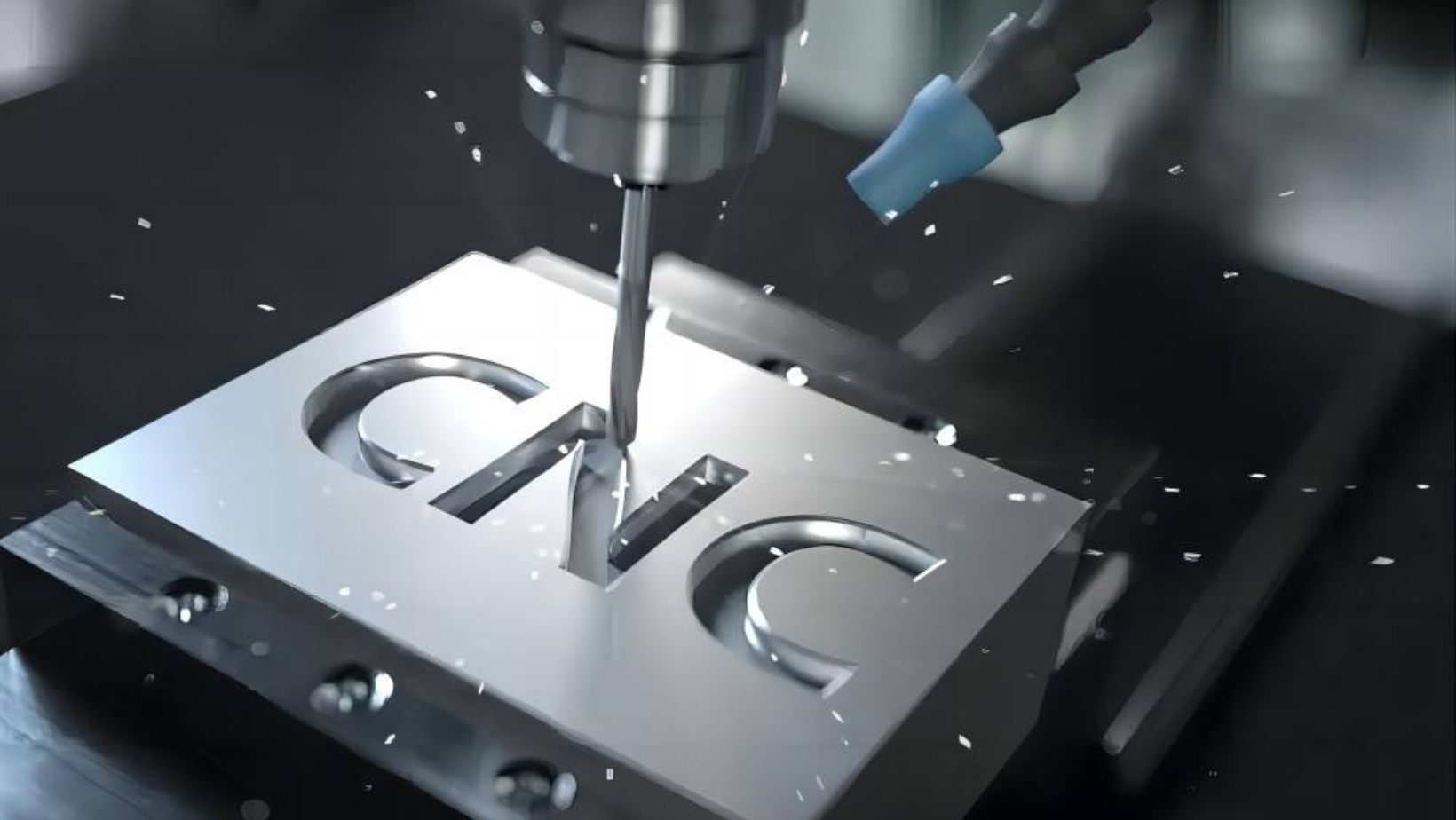
Errors and imperfections are minimized, so resources aren’t wasted. Once the design is finalized, CNC machines can quickly shift to mass production without losing a beat.
How CNC Prototypes Compare to 3D Printing
Many people wonder if 3D printing has replaced CNC machining. After all, 3D printing is often seen as the go-to method for rapid prototyping. However, CNC and 3D printing serve different purposes, and CNC prototypes still have an edge in several ways.
Material Strength and Durability
3D printing is great for creating complex geometries, but the material strength can be lacking. CNC machining produces stronger prototypes because it uses solid blocks of material, whereas 3D printing layers can lead to weak spots. For projects where strength is key, CNC is the better choice.
Surface Finish
CNC prototypes often have a superior surface finish compared to 3D-printed parts. CNC machines cut material cleanly, leaving behind smooth surfaces. This is crucial for prototypes where aesthetics matter or when the part will undergo additional processing like painting or coating.
Higher Production Volume
If you need multiple prototypes, CNC machines can handle it with ease. They can produce the same part repeatedly with high precision, making them ideal for low to medium production runs. In contrast, 3D printing is often slower for higher volumes, making it less ideal when you need consistency in larger numbers.
The Impact of CNC Prototypes on Various Industries
CNC machining has found its way into a broad range of industries. Here’s a look at how CNC prototypes are making an impact:
Automotive
In the automotive world, time is of the essence. Car companies use CNC prototypes to test parts quickly, from engine components to interior fixtures. The speed and accuracy mean fewer delays in bringing a car from concept to showroom. Prototypes can be tested under real-world conditions, ensuring they meet safety and performance standards.
Aerospace
Aerospace companies rely heavily on CNC prototypes due to their need for exact precision. In an industry where safety is critical, having a prototype that matches the final product is vital. CNC machines allow engineers to make minute adjustments quickly, fine-tuning parts before production.
Medical
Medical device manufacturing requires strict standards. There’s little room for error when making parts for surgical tools or implants. CNC prototypes enable companies to meet these high standards by providing accurate and reliable models that can be thoroughly tested.
Consumer Electronics
For consumer electronics, design and functionality need to go hand-in-hand. CNC prototypes help tech companies test everything from enclosures to internal components.
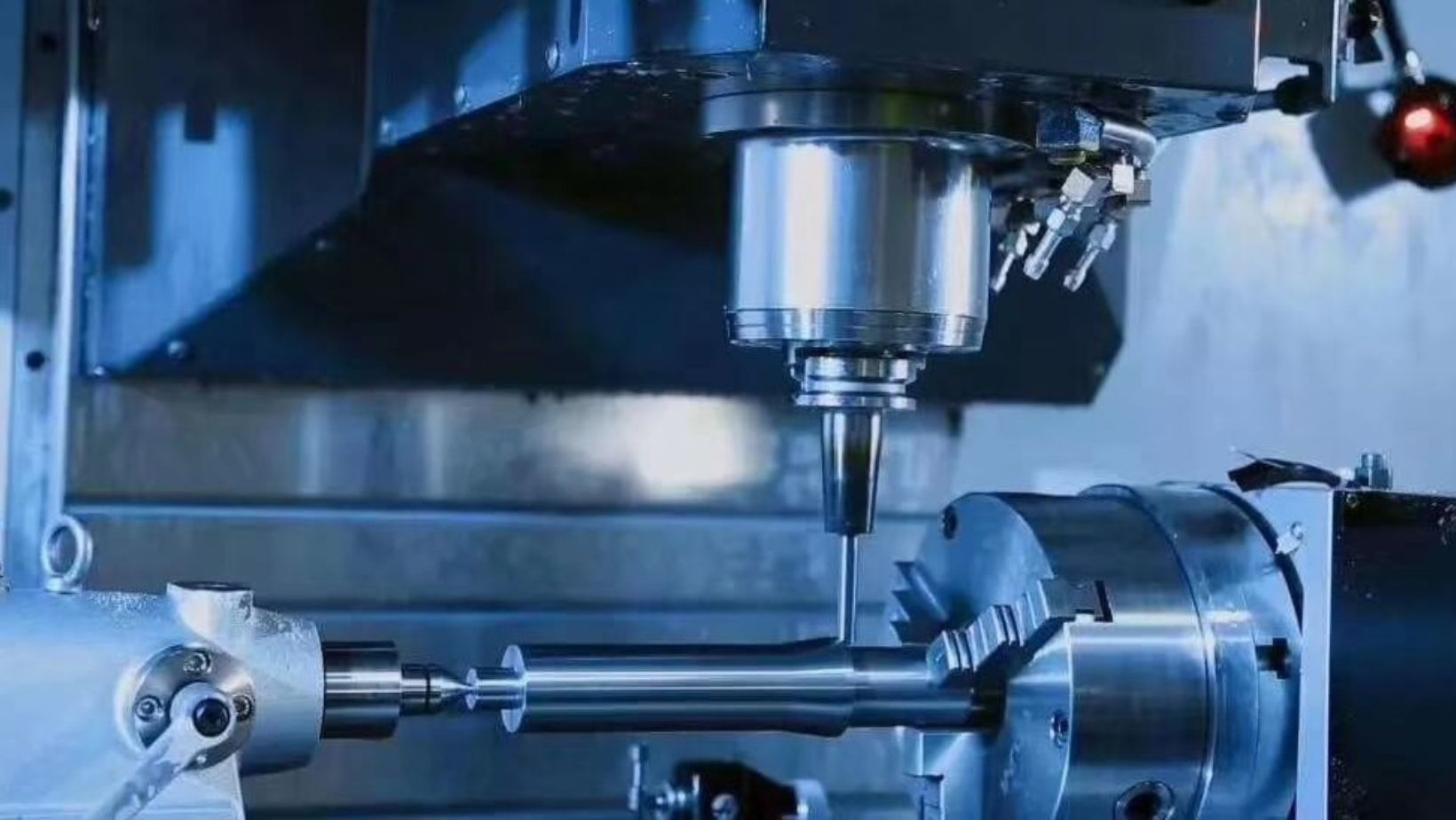
The ability to iterate quickly means companies can adjust designs based on feedback and market needs, staying ahead of competitors.
The Challenges of CNC Prototyping
While CNC prototypes offer many benefits, they aren’t without challenges:
Initial Costs
The setup cost for CNC machining can be higher than other methods, especially if you need complex machinery. However, the long-term savings often offset this initial investment.
Material Waste
CNC machining is subtractive, meaning it cuts away material from a larger block. This can lead to waste, especially with expensive materials. Manufacturers often try to optimize material usage, but it remains a consideration.
Programming Complexity
Programming a CNC machine requires skill. Creating the code for complex parts can be time-consuming and requires experienced technicians. Errors in programming can lead to costly mistakes, making it important to get it right from the start.
CNC Prototypes: Not Just for Big Companies
While CNC prototyping is often associated with large companies, smaller businesses and startups are also jumping on board. Access to CNC machines is more affordable than ever, thanks to advances in technology and a competitive market. Many CNC service providers offer on-demand prototyping, so companies don’t need to invest in their own machines. This lowers the barrier to entry, allowing innovators of all sizes to use CNC prototypes.
Future Trends in CNC Prototyping
CNC technology continues to evolve. Innovations in software, hardware, and materials are driving the industry forward. Some of the trends to watch include:
Improved Automation
New CNC machines are becoming more automated, reducing the need for manual intervention. This speeds up the process even further and decreases the chance of human error.
Advanced Materials
The range of materials that CNC machines can handle is expanding. This includes hybrid materials that offer strength, flexibility, and lightweight properties, ideal for specialized applications.
Integration with Other Technologies
Combining CNC machining with other technologies, like 3D printing and laser cutting, is becoming more common. This hybrid approach allows for even more complex prototypes and innovative designs.
Why CNC Prototypes Are Here to Stay
The role of CNC prototypes in product development isn’t just a passing trend. Their precision, speed, and versatility make them a core component in various industries. Companies that need to move fast, minimize errors, and ensure high-quality outcomes are turning to CNC technology. As the demands of the market grow, CNC prototypes will continue to adapt, meeting new challenges head-on.
In a world where efficiency and accuracy are paramount, CNC prototypes stand out as a reliable choice. They offer the kind of consistency and durability that can’t be easily matched, making them the future of rapid prototyping.